Lime Rendering & Wall Stabilization
Grade 2 Listed Church
Warton, Lancashire
Grade II Listed St Oswald’s Church stands in the heart of the Lancashire village of Warton and has served the local population for over 600 years. There has been a church on the site for over 1000 years and the ruined remains of the medieval rectory still survive. The tower was built in 1480 and paid for by the local Washington family who were ancestors of George Washington. This US connection attracts tourists to the church and the American flag is flown from the tower on 4th July each year.
We firstly erected scaffolding on the chancel gable and flank walls. This scaffold included retractable transoms to allow for access during the rendering process. Some of the issues recorded by our structural engineers, Curtins, included two large cracks above the tracery arch and the outer arch section had started to rotate outwards. As a result, it separated from the internal masonry curvature. One of the initial tasks was to install needle propping above the arch which involved installing bracer timber and scaffolding clamps. This was a challenge due to the 750mm thick walls and it took approximately two weeks to core out twelve holes in the masonry to install the needles.
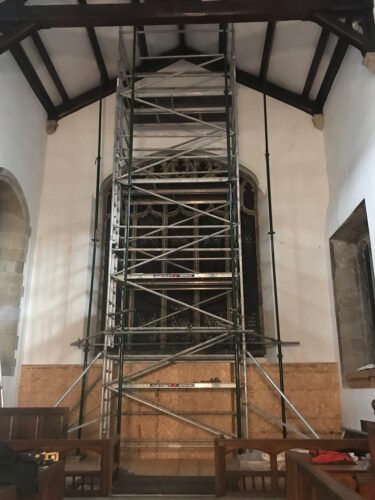
Secondly, in order to safeguard the internal walls and chancel floor, we installed protection, including a dust curtain, to prevent dust migrating into the nave. Once the needles were in position, we removed the gable copings and stripped back the slate roof to allow the dismantling of the masonry. We disassembled down to the arch to enable us to carry out structural works to the rotating outer arch. All the copings and masonry were lowered to the ground using a scaffolding hoist due to the weight it would impose on the scaffolding structure.
Bespoke Tie Bar Fabrication
With the masonry dismantled, we then cleared the joints of the voussoirs. Following this, we grouted them with a mix of NHL 5 hydraulic lime, prompt, and fine aggregates. Other areas of the tracery arch windows also required grouting as the joints had eroded over time. To solve this, we created some unique stainless-steel tie bars in our fabrication workshop comprising of threaded bar that would be drilled into the inner arch with a welded cramp to fix to the outer arch. Then we formed a groove in the outer arch to accommodate the cramp and having made a mould from modelling clay we poured molten lead into the cramp pocket. This would hold the cramp firmly to the outer arch for the future.
Once all eight voussoirs had been cramped we started the rebuilding of the gable pike. Next, we used hot mixed lime mortar for the masonry work and bespoke stainless-steel wall ties were fabricated from 9mm helical bar to tie the internal and external walls. The centre of the wall had packing installed with a little lime mortar to bind. This packing was then carefully laid to ensure the maximum bond between the masonry leaves.
Dismantling The Nave Parapet
The project also involved the dismantling of the nave parapet due to internal water ingress. We dismantled the three sections of masonry parapet after recording the existing layout and fabricated Code 5 lead cover trays on site, the first of which was to run alongside the lead roof gutter and under the masonry to turn the water out of the wall. The second tray was installed below the coping and flashed to the roof gutter. Then tlead was painted with two coats of bitumen paint and coated with a fine sand. As a result, the bitumen prevented the lime mortar from eroding the lead and the sand, enabling the lime mortar to grip the lead. Each course of masonry was pinned together with stainless steel bars.
We fixed the bars into the lower stone using epoxy resin. Lead collars were then lead-welded onto the tray to prevent water ingress around the bars. The top stone was cored out to accept the bar and collars, no epoxy resin was used here to allow dismantling of the parapet at a later date. The parapet was rebuilt using lime mortar. We used a hot mixed lime mortar blended with a hydraulic lime which was used hot. Our restoration technicians ensured the vertical joints were fully mortared with the minimal joint size and the excess lead was trimmed from the parapet then neatly dressed to the masonry. All corners were lead-welded to ensure a water-tight seal.
Chancel Gable Rebuild
The mortar was removed from the chancel, revealing large voids in the masonry where the original lime mortar had decayed. Using a hot mixed lime mortar, we packed and filled the voids in the masonry. Pinning stones were required where the voids were large, and we applied a heavy gauge pointing to the masonry ready to receive the two harl coats. The mortar for the coats was also hot mixed lime mortar gauged with a hydraulic lime. Three coats of hot-mixed lime wash were subsequently applied to the render.
Stone Repair
Finally, the voussoirs on the tracery arch were repaired, where water penetration to the joints had caused erosion to the stone. We installed carbon fibre armatures to the projection followed with stainless steel wire being wrapped around the carbon fibre to create a tie. Stone repair mortar was then worked up in layers and tooled back to reform the voussoirs profile.
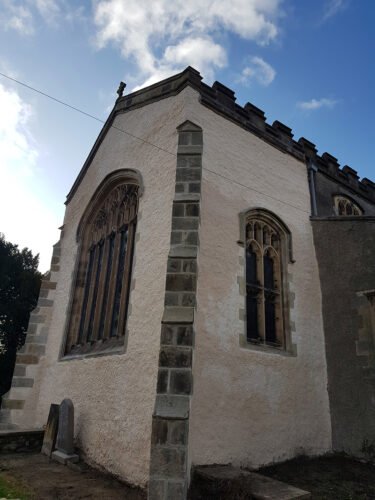
Rev. Robin Figg said: “It was a pleasure to work with both HPA Architects and UK Restoration Services on the chancel repair project at St Oswald’s Church. As custodians of the grade II listed building, the Parochial Church Council was mindful of its responsibility to ensure a high standard of work was carried out to help ensure the future of this important feature within the local community. We were impressed throughout the project with the high standard of craftsmanship by the UK Restoration Services team as they worked on the stone, lead and lime rendering. We look forward to involvement with UK Restoration Services in further repair work on the church building.
Don’t forget to keep yourself updated with our projects on our YouTube channel